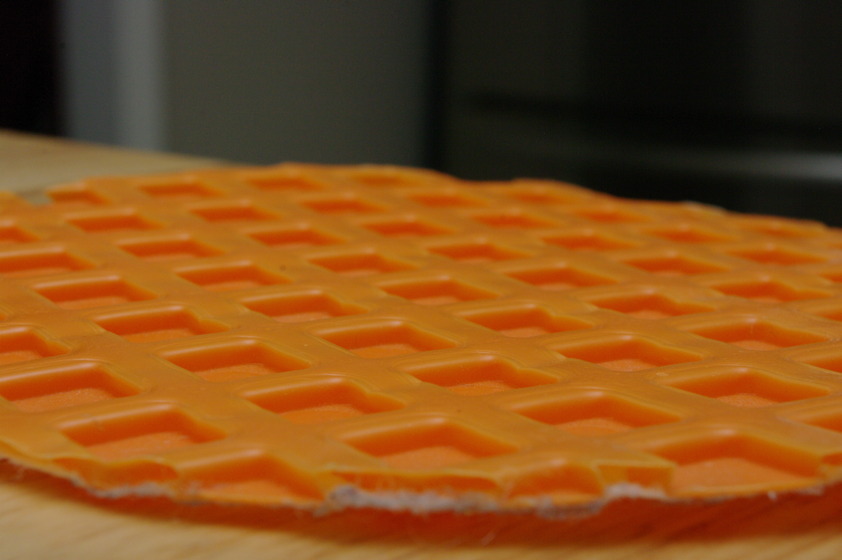
The scratch coat method
One of the most common and outdated ceramic floor practices used today is the scratch coat method on top of sub-floors and wood joists. Some people call it the “Jersey mud job”. This seems to be the most common practice in Toronto for ceramic floors, and maybe Ontario as well. Failure rates are relativity high within 5 to 10 years from what I have seen with some homes. Homes with a decent sub-floor do last longer. Why is this outdated method used? The simple answer is construction economics and the use awareness of the use of uncoupling membranes is still not known by homeowners and most contractors. The flooring trades in Toronto’s housing sector have a scratch coat culture that appears to be difficult to shake.
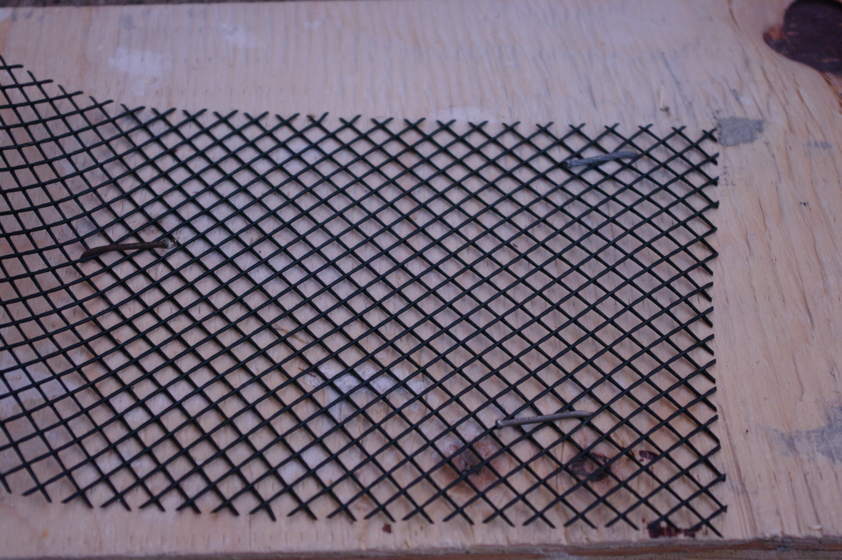
The scratch coat method secures the the ceramic tiles to the sub-floor and joists as best as possible. It is the philosophy of maximum control of your building components and structure as a whole. The firmer, the better. This is similar to the philosophy of maximum vapour control of using polyethylene vapour retarders (barriers) anywhere you think you are controlling the movement of water vapour, which not surprisingly also doesn’t work that well. The scratch coat is installed by using a sheet of metal wire that sort of looks like chicken mesh and nailing it down to the plywood sub-floor. The nails are installed between the mesh and purposefully bent over top the mesh as to hold the mesh down tight to the sub-floor. Thin set mortar is forced between the mesh, and when it sets, ceramic tiles can be installed as they have something else ceramic to bond to as it can’t bond to the metal. The steel mesh was thought to control the expansive forces, removing the possibility of cracks.
The reason for this type of practice from what I have heard from installers is that they believe it is similar to the function of re-bar in concrete. Many people assume that this is a good method because it “controls” the movement of ceramic tile, whatever that means. We have all seen ceramic tiles in various houses where the tile has de-laminated from the floor and has become loose at the grout or the tile has cracked in half. When I ask a homeowner why do you think this happened, the assumption I often hear is somehow the tiles were not tightly adhered to the floor with cheap materials and a lot of mostly dumbfounded looks. Although substandard material failures do happen, most often it not always the underlying reason why the floor tiles crack or de-laminate. As I have mentioned in previous articles, your house moves for various reasons and ceramic products such as tile and grout don’t handle expansive forces well and must be taken into account when installing any new component in your home.
Lets look at the physics on why this total control philosophy doesn’t really work a little later on.
This is a cross section of a ceramic tile floor
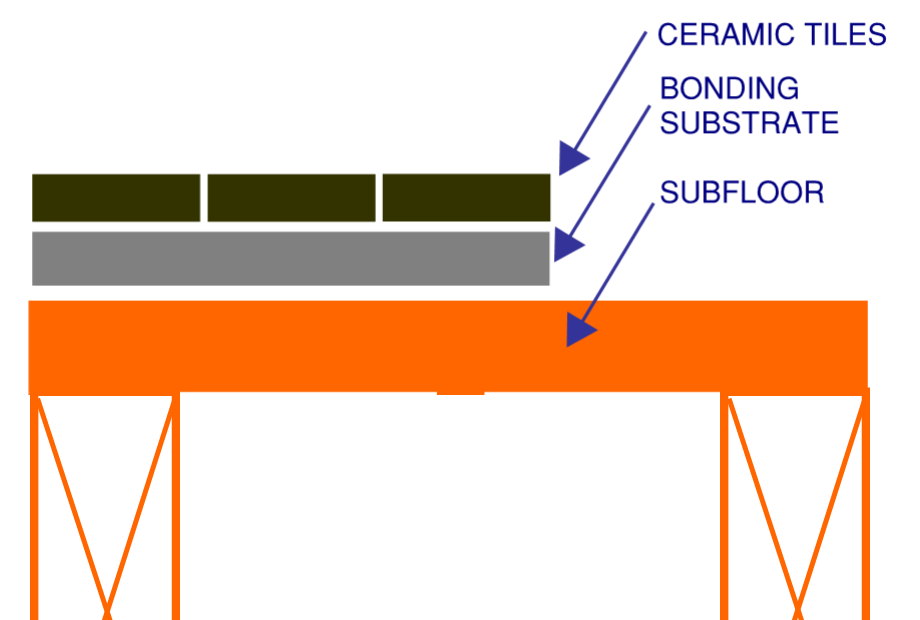